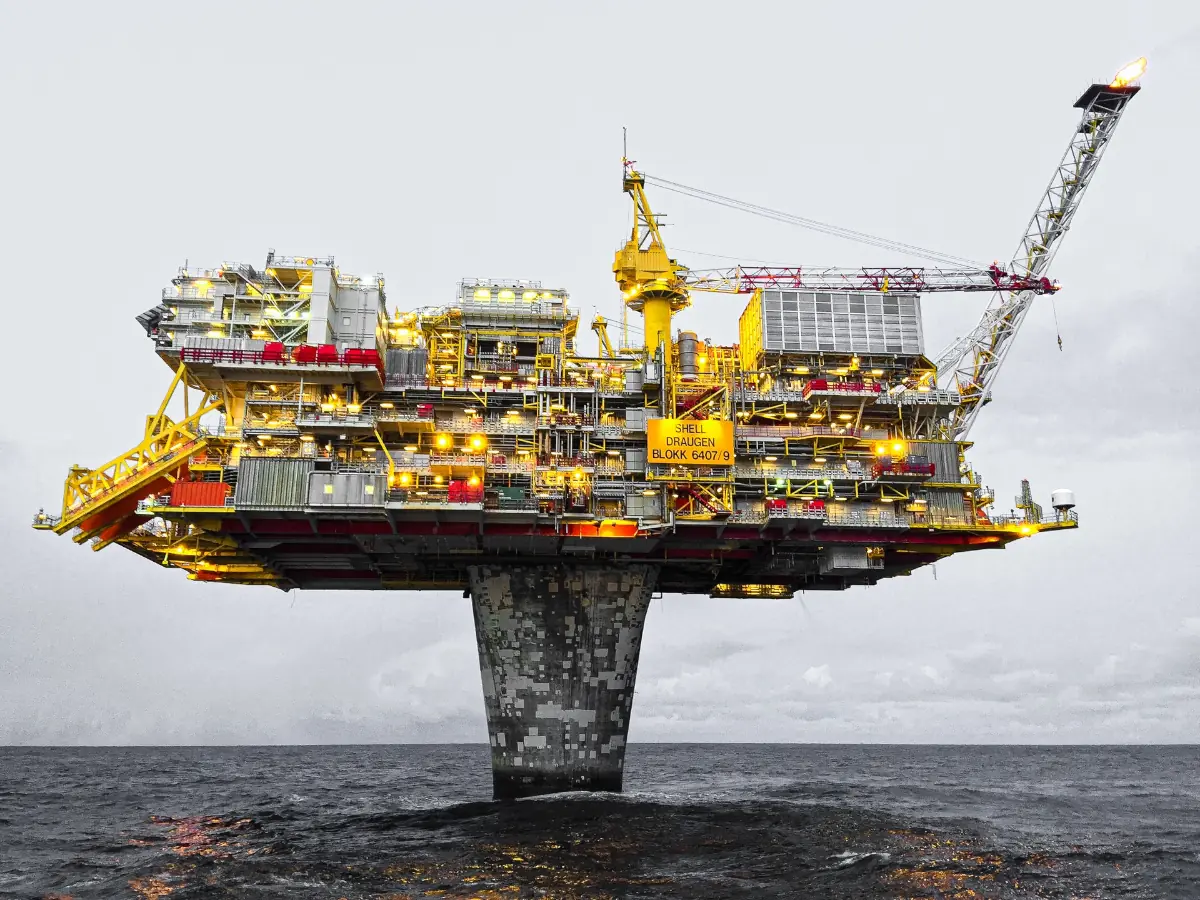
To prevent uncontrolled flow of fluids during well drilling tasks and damage to the environment or dangers to people, due to exposure to hydrocarbons, several measures are used, including the BOP (Blowout Preventer).
BOP is a mechanical barrier high-pressure safety valve, utilised for land rigs and jack up tasks; it is the most efficient physical barrier currently employed.
A blowout is an uncontrolled flow of fluids or gas migration that occurs when deposits of oil and/or natural gas can flow into the atmosphere at the surface; it is also known as a Loss of Well Control (LOWC).
Natural deposits of oil and gas are contained in rock formations, in the earth’s crust, called reservoirs. Oil and natural gas fields have high pressures and temperatures.
The first barrier against the high pressure fluid spill is the drilling muds. These are water and oil based products, sufficiently heavy, which create a hydrostatic pressure or weight downward in the reservoir, higher than the pressure of the deposits. The effect is also called “heavy mud to kill well”. The mud flows down the drill pipe, a high-strength steel pipe used in drilling.
If the pressure inside the deposit is higher than the mud hydrostatic pressure, a well control problem occurs, called “kick”. An uncontrolled kick can even lead to an uncontrolled “blowout”.
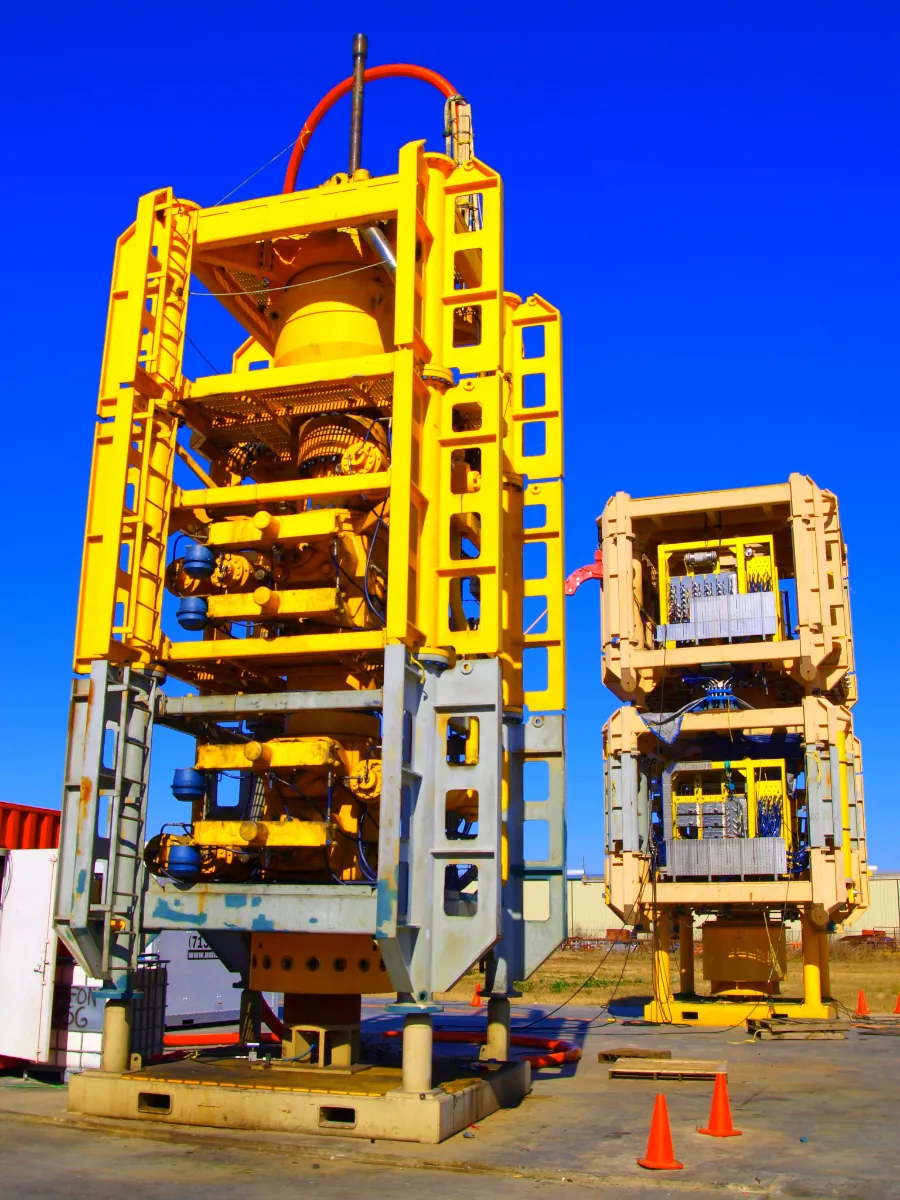
A BOP has several functions such as carrying out well pressure tests, injecting and removing fluids from the well through “choke” and “kill” lines, but the most important is the ability to prevent blowouts of hydrocarbons from the well.
The BOP includes components such as electrical and hydraulic lines, kill line, choke flowline, valves, hydraulic accumulators, test valve, control pods, hydraulic connectors, riser joint.
The BOP is installed on the sea floor at the top of the wellhead, includes valves and rams, that can be closed when an uncontrolled flow of fluid in the wellbore occour. Its purpose is to seal an open wellbore and surrounds the drill string, with drilling equipment going through it into a well. The BOP stack includes two types of preventer such as the ram-type and the annular-type. The ram-type provides four or more ram preventers, it is able to completely seal the well and prevent well fluids from escaping to the surface through the inside of the drill pipe. By integrating the annular preventer with the ram type, the well control capacity and plant safety will be increased. In other words, the annular preventer is a valve hydraulically operated, used to seal the space around the drill pipe, to control and monitor the fluids of the well. The subsea BOP provides two annular preventers.
Onshore and Offshore BOP can be activated manually or operated by hydraulic pressure, mechanically through the ROV vehicle, with electrical and acoustic signal. It can also be activated automatically in the event of a loss of power or of hydraulic pressure.
The fluid that operates the subsea BOP valves comes from the rig through an umbilical.
The subsea BOPs have been equipped with electrohydraulic multiplex (E/H MUX) and microprocessors. New technologies such as electric BOP are currently being studied to make the structure more reliable and capable of reducing downtime.
An electric BOP is a lighter structure, partially eliminating the hydraulic equipment, which causes weighting and fatigue on the wellhead. In addition, the surface equipment, used to control underwater hydraulic devices, is also reduced. The use of batteries compared to hydraulic accumulators can improve overall efficiency and save space and weight.
Jessica Moro
DSO
Image
Cover: pexels-janrune-smenes-reite-3216911, Foto di Jan-Rune Smenes Reite da Pexels
Article: Subsea Blowout Preventer (BOP), by Matthew Colvin de Valle, from flickr.