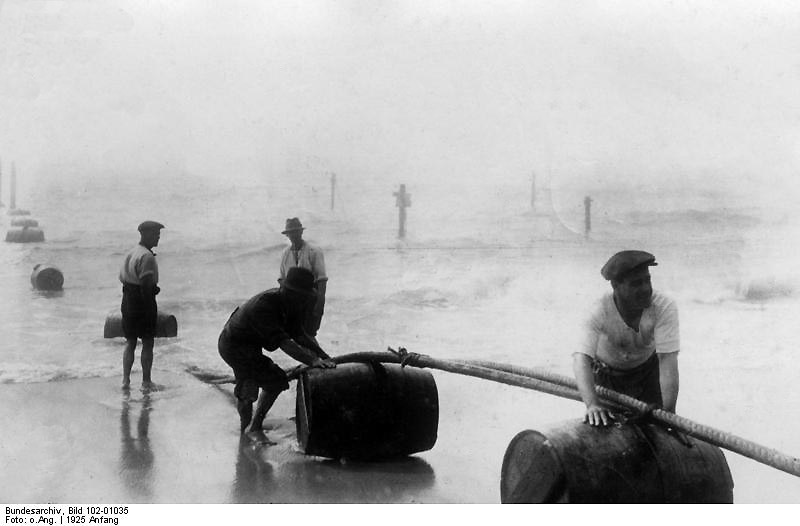
New-York. Eine Kabel-Legung, Italien-Amerika. In Rockoway Beach wurde das Ende eines neuen Unterseekabels an Land gezogen, welches New-York mit Süd-Europa verbinden soll. Es ist das erste direkte Kabel zwischen den Vereinigten Staaten und Süd-Europa. Es läuft von New-York zu den Azoren und von dort über Malaga in Spanien nach Rom. Das Bild zeigt das Anlandziehen des Kabels in der Nähe New-Yorks. Die Gesamtlänge dieser neuen Verbindung beträgt 4704 Seemeilen.
Cables and pipelines are fundamental to the global economy, since they allow telecommunication and carry electricity and Oil&Gas products.
To ensure the good conditions of pipes and cables the preparation of the seabed is of crucial importance; it must be as flat and regular as possible, otherwise, if the seabed is irregular, conductors will suffer the risk of overstressing.
Sea currents and tides are the main interacting factors with seabed; they can cause the scouring and spanning of the cable or pipeline, which will twist and bend till breakage.
To avoid damages due to seabed modelling or cave in, it is necessary a planned and periodic inspection and control activitiy, in order to detect any change and immediatly carry out stabilisation tasks.
Subsea Cables
There are fiber optic and electical subsea cables.
Electrical cables transport energy power generated by an offshore plant to the onshore electricity grids o landing station. These cables can be anything from 70mm to 210mm in diameter and come in AC or High Voltage AC and High Voltage DC.
Fiber-optics cables are vital infrastructure, enabling telecommunications and the Internet. They are larger from 12 to 17mm, but considering protective wire armouring their diameter may increase up to 50mm.
There are many cables on the seafloor, nearer to the shore cables are buried under the seabed for protection, in the deep water they are laid directly on the seabed. However, cables can be laid on the seabed surface even in shallow water, where the seabed is not suitable for burial, such as in areas of rocky outcrop and high ecological sensitivity.
Cables can be exposed to strong currents and the action of waves that are capable of carrying and moving sediments in its vicinity and in some cases they may undermine and bury the cables. In addition the environmental effects create suspensions and strum. The tidal current that causes the erosion of sediments and sands under the seabed surface cable is called scouring and causes its suspension with the risk of torsion and oscillation.
Cable Inspection Techniques
It is essential to track the cable route in order to inspect the condition of the surface seabed or buried cable. For the underwater cable detection the underwater camera, side scan sonar, sub-bottom profiler and magnetic sensors are used. Magnetometers can be used to locate a cable in a trench or buried by sediment, as it detects the magnetic fields induced by power transmission cables.
A common method used to inspect a subsea cable is visual inspection, which can be accomplished through an AUV system equipped with an HD digital still cameras. AUV cable inspection will be conducted at a suitable height directly above the cable, dependent on conductor diameter.
Subsea Pipeline
Subsea pipelines play a particularly important role in the exploitation of offshore oil and gas resources, since they are used to transport oil from the production area to the export oil terminal, or to a refinery process plant where crude oil is transformed.
They could be considered as the most preferred method of transportation of petroleum fluids by safety, economic and environmental point of view.
Pipelines can be damaged because of abrasion and corrosion, shipping incidents or falling objects.
In addition the unsupported pipeline can suffer from fatigue, as is the case with free spans or sections of the pipeline that are not touching the seabed, caused by a rough seabed or scouring action of water and sand. Subsea pipelines with major free spans, if not treated in time, may lead to fatigue damage to the pipelines, causing oil and gas leakage.
The consequences of pipeline leakage are destructive for marine ecosystem, economic loss and environmental cost.
Pipelines and Cables should be designed strong and reliable enough to resist impacts (waves, current flow, vibration, corrosion) from both nature and human activities.
Therefore, appropriate inspection, monitoring and assessment tasks to ascertain their conditions are essential.
Pipeline Inspection Techniques
The Remotely Operated Vehicle (ROVs) and autonomous underwater vehicles (AUVs) are used for continuous monitoring, assessment of pipeline integrity and evaluation of the seafloor.
In regards to subsea pipeline inspection, the first and the simplest method of inspection is, of course, General Visual Inspection (GVI) or Close Visual Inspection (CVI). The pipeline inspection includes external inspection and internal inspection. In this article, the external inspection techniques are discussed. The subsea pipeline internal inspection is carried out through non-destructive testing techniques and pigging technology.
To inspect pipelines through the ROV vehicle by adopting the GVI technique, it is suitable to place three cameras on it, one in the centre at the bottom of the vehicle frame and one on each side (left and right). The left and right cameras may be placed on booms to observe below the pipeline and the area between the pipeline and seabed.
Another test consists in verifing if there is any leakage.
Leak monitoring can be done through the Acoustic Leak Detection (ALD) system, that uses passive acoustic hydrophone technology to detect and locate underwater fluid leaks by distinguishing the noise of a leak from other sound sources.
Other acoustic tools could be used to identify a pipeline (in a similar way the magnetometers are utilised to locate pipeline on the bottom or buried), SBES/MBES/SSS and SAS devices are used for bathymetric mapping and visualizing the seabed and objects on seafloor, Sub-Bottom Profiling (SBP) can map the depth and location of buried pipeline providing a measure of material below the seabed or sediment coverage.
Several of these instruments may be diver-held or mounted on an ROV, AUV, or PIG.
Paolo Mazzone
SubEng – HSE Adviser
Image:
Cover: New York, Verlegen von Unterseekabel, 1925, German Federal Archive